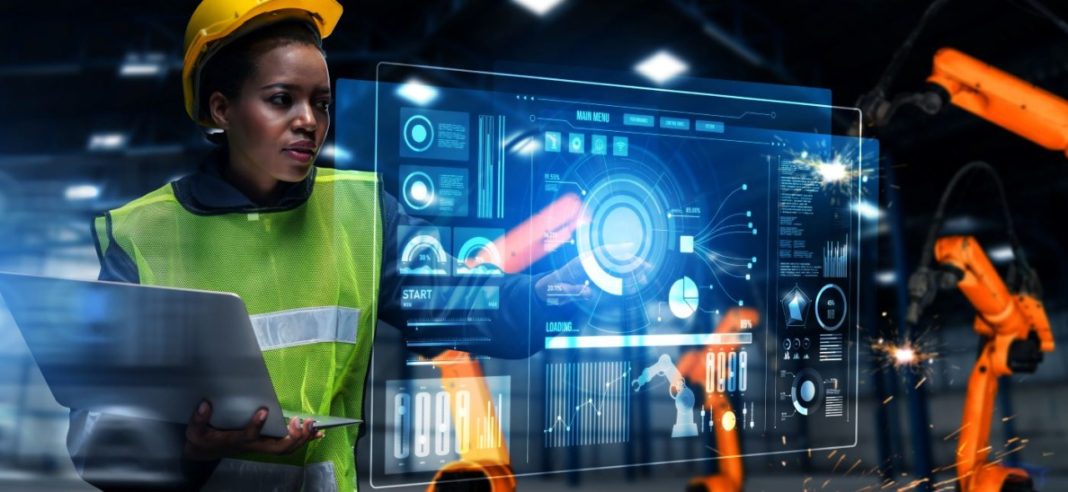
Uma pesquisa inédita da Confederação Nacional da Indústria (CNI) com mais de mil empresas revela que a indústria está mais digital do que há cinco anos. Se em 2016, menos da metade (48%) fazia uso de tecnologias digitais, em 2021 esse percentual foi de 69%.
Contudo, a maioria utiliza uma baixa variedade de tecnologias, indicando que se encontram em uma fase inicial do processo de digitalização: 26% utilizam de uma a três das 18 tecnologias listadas, e apenas 7% adotaram 10 ou mais delas. Para 37% das empresas, a falta de profissionais qualificados é uma barreira externa para adoção de tecnologias digitais.
De acordo com Ana Paula Kubinhets, CEO da Aquarelle, integradora de tecnologias para indústria 4.0, a inteligência artificial (IA) evoluiu para identificar problemas com precisão e agir. O tempo de inatividade pode custar a um fabricante de automóveis, por exemplo, mais de US$ 21.000 por minuto.
“Essa tecnologia avançada permite que as empresas adicionem facilmente “olhos” inteligentes às suas operações e monitorem remotamente os ativos com dispositivos móveis padrão como smartphones e tablets”, explica.
O desafio é como fazer a transição de um ambiente reativo – onde a maioria dos fabricantes está – para um ambiente proativo. Muitas pessoas falam sobre a Indústria 4.0, mas tem dúvidas sobre como começar e como integrar as tecnologias, como antecipar problemas a serem corrigidos antes que eles realmente se tornem problemas.
Da teoria para a prática
Segundo a especialista em indústria 4.0, começar com a detecção de defeitos é uma boa maneira de entrar em um ambiente de IA que é simples de entender.
“Primeiro o sistema vai capturando dados, seja de sensores ou dados visuais (imagens), e obtendo visibilidade sobre o que os ativos estão fazendo. É fácil ver que o sistema está fazendo um trabalho melhor do que um indivíduo pode fazer. Depois que se cria confiança nesses resultados, fica mais fácil usar o aprendizado de máquina e a tecnologia de IA para manter os ativos em execução no chão de fábrica, entender a saúde dos ativos, o ciclo de vida, e ter uma visão única dos ativos em toda a empresa. Por fim, os modelos de IA se unem para permitir que a empresa veja onde há probabilidade de falha para todos os seus ativos e tome medidas preventivas. É uma evolução”, diz Kubinhets.
À medida em que a IA vai evoluindo e as empresas passam a gerenciar seus ativos de forma inteligente, elas buscam o Zero D – que significa zero defeitos e zero tempo de inatividade – e a resiliência para a manufatura e diversos setores como o de viagens, transporte, trens de carga, infraestrutura civil, com pontes e estradas.
Kubinhets explica que esse conceito considera que ambos os tópicos – defeitos e tempo de inatividade – não devem ser abordados separadamente. Porque qualquer um deles é crítico. Uma indústria alcança a verdadeira transformação quando ataca os dois tópicos juntos. Porque não importa quão alta seja a qualidade de produção de uma empresa. Se ela tiver tempo de inatividade, não poderá atender bem as demandas. Por outro lado, mesmo que uma indústria seja supereficaz em seus processos de fabricação, se sua inspeção de qualidade for ruim, ela estará apenas aumentando seu retrabalho.
Portanto, se a empresa puder combinar a inspeção visual, utilizando modelos de visão computacional focados na inspeção de qualidade, com uma plataforma de gerenciamento de desempenho de ativos para reparo preditivo, ela vai conseguir aumentar a qualidade e a eficiência da produção ao mesmo tempo, e isso ajuda a construir um negócio sustentável e resiliente.
“Alguns fabricantes já estão caminhando para isso e vendo resultados imediatos. Uma montadora de carros norte-americana, por exemplo, encontrou 30 defeitos nos primeiros 30 dias, o que não é grande coisa. Mas ela estava olhando para um único conector em um ponto de sua instalação, vinculado a um problema específico. Quando isso foi expandido para vários locais em sua linha de montagem, encontraram até 200 defeitos por dia. Assim, no primeiro mês, fizeram uma economia de US$ 1,8 milhão nessa linha de fabricação”, relata Ana Paula Kubinhets.
No Brasil, a mesma pesquisa da CNI (Confederação Nacional da Indústria) citada anteriormente mostra que, em 2021, o setor automotivo foi o que adotou maior variedade de tecnologias digitais: 35% das empresas utilizam pelo menos sete entre as 18 tecnologias digitais avaliadas.
Além da indústria automobilística, muitos setores podem se beneficiar, como por exemplo, o segmento de viagens e transporte. “Considerando as ferrovias e os ativos – que são os trilhos da ferrovia e o próprio trem -, os dados do sensor podem ajudar a encontrar possíveis falhas, mas a inspeção visual de IA também pode ser usada para inspecionar visualmente vagões, desgaste em acoplamentos, rodas, fiação, etc.”, diz Kubinhets.
O fato é que quando uma empresa tem conhecimento do que realmente precisa ser corrigido, ela não precisa verificar tudo uma vez por semana. Existe a ideia de que os horários de manutenção frequentes são mais baratos, mas eles podem ser um exagero.
Com uma plataforma que concilia dados visuais e dados de sensores, fornecendo monitoramento da integridade dos ativos durante 24 horas por dia, 7 dias por semana, é possível detectar anomalias antes que se tornem problemas críticos e prever a probabilidade de falha no futuro.
“Com isso, os técnicos, que estão se tornando um recurso escasso, podem programar melhor seu tempo. Porque a empresa terá os dados que indicam que esses ativos estão bem e não vão falhar por mais um mês, vários meses ou até anos. E os técnicos poderão ser utilizados com muito mais eficiência nas áreas de maior valor, com base em dados em que podem confiar”, conclui a CEO da Aquarelle.